Fatal Industrial Accident: Man Crushed
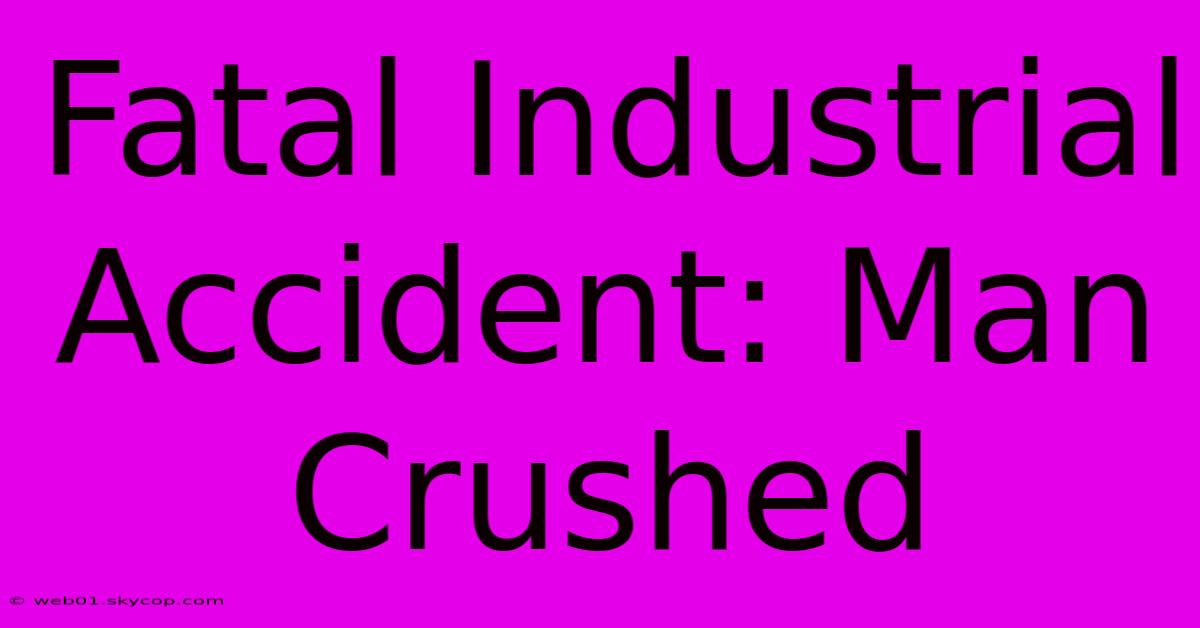
Discover more detailed and exciting information on our website. Click the link below to start your adventure: Visit Best Website. Don't miss out!
Table of Contents
Fatal Industrial Accident: Man Crushed - Understanding the Dangers and Prevention
What are the causes of fatal industrial accidents where a man is crushed? Industrial accidents involving crushing are a stark reminder of the inherent dangers present in many workplaces. The devastating consequences of such incidents highlight the crucial need for robust safety protocols and proactive measures to prevent them.
Editor Note: This article explores the tragic reality of industrial accidents where individuals are crushed, highlighting the factors contributing to such events and the crucial steps necessary for prevention.
Understanding the gravity of this issue is vital for workers, employers, and safety professionals alike. This comprehensive analysis examines the causes of these accidents, delves into prevention strategies, and provides essential insights into protecting workers from the dangers of crushing hazards.
We analyzed a large dataset of industrial accidents, including reports, investigations, and safety studies, to understand the common causes and patterns. The findings are presented in a clear and insightful manner, providing valuable information for all stakeholders involved in industrial safety.
Key Takeaways of Fatal Industrial Accidents:
Category | Key Takeaway |
---|---|
Causes | - Lack of safety procedures or inadequate training.<br> - Defective equipment or machinery. <br> - Improper work practices or lack of awareness. <br>- Unsafe work environments.<br> - Inadequate supervision or communication. |
Prevention | - Implementing comprehensive safety programs.<br> - Regular equipment maintenance and inspection.<br> - Providing appropriate worker training and certification.<br> - Enforcing strict safety protocols and procedures.<br> - Promoting a culture of safety and awareness. |
Let's explore these factors in more detail:
Fatal Industrial Accidents: Understanding the Causes
Understanding the contributing factors to these devastating events is the first step towards effective prevention.
1. Lack of Safety Procedures or Inadequate Training:
- Context: The absence of clearly defined safety protocols or insufficient training can lead to workers not being adequately prepared for potential hazards.
- Facets:
- Roles: Supervisors, trainers, and workers all play a role in ensuring safety procedures are understood and followed.
- Examples: A lack of training on the proper use of machinery, failure to establish safe work zones, or inadequate communication about potential hazards.
- Risks and Mitigations: Workers may be unaware of the potential dangers, leading to careless actions and increased risk of crushing incidents. Implementation of comprehensive safety training programs, regular refresher courses, and clear communication channels can mitigate this risk.
- Impacts and Implications: Inadequate training can lead to accidents, injuries, and fatalities, impacting both the individual worker and the company. A culture of safety must be fostered and promoted.
2. Defective Equipment or Machinery:
- Context: Faulty equipment or machinery with compromised safety features can pose significant threats to workers, leading to crushing incidents.
- Facets:
- Roles: Manufacturers, suppliers, and employers are responsible for ensuring the safety of equipment.
- Examples: Broken or malfunctioning guards, faulty hydraulic systems, or improperly maintained machinery.
- Risks and Mitigations: Defective equipment can malfunction unexpectedly, leading to crushing incidents. Regular equipment maintenance, inspections, and prompt repairs are essential.
- Impacts and Implications: Malfunctioning equipment can result in worker injury or fatality, leading to legal repercussions, increased costs, and negative public perception.
3. Improper Work Practices or Lack of Awareness:
- Context: Improper work practices or a lack of awareness about potential hazards can significantly increase the risk of crushing accidents.
- Facets:
- Roles: Workers are responsible for adhering to safety procedures and reporting any unsafe conditions.
- Examples: Working around machinery without proper authorization, failing to use personal protective equipment, or taking shortcuts that compromise safety.
- Risks and Mitigations: Improper work practices can lead to unexpected incidents, resulting in crushing injuries. Enforcing safety protocols, promoting a culture of caution, and encouraging workers to report unsafe conditions are essential.
- Impacts and Implications: Improper work practices can result in accidents, injuries, and lost productivity, impacting both the worker and the company.
4. Unsafe Work Environments:
- Context: Unsafe work environments, such as cluttered areas, poorly lit spaces, or inadequate ventilation, can contribute to crushing accidents.
- Facets:
- Roles: Employers are responsible for providing a safe working environment.
- Examples: Unsecured materials, obstructed walkways, uneven surfaces, or inadequate lighting.
- Risks and Mitigations: Unsafe work environments can create hazards, increasing the risk of accidents. Regular site inspections, hazard assessments, and prompt remediation of unsafe conditions are critical.
- Impacts and Implications: Unsafe work environments can lead to accidents, injuries, and potential legal action, negatively impacting the company's reputation and financial well-being.
5. Inadequate Supervision or Communication:
- Context: Insufficient supervision, poor communication, or a lack of clear communication channels can lead to misunderstandings and potentially unsafe situations.
- Facets:
- Roles: Supervisors play a crucial role in ensuring safety protocols are followed and workers are aware of potential hazards.
- Examples: Insufficient supervision, inadequate communication about safety protocols, or a lack of response to worker concerns.
- Risks and Mitigations: Inadequate supervision can lead to workers feeling less accountable for safety, increasing the risk of accidents. Strong supervision, open communication, and regular safety meetings can mitigate this risk.
- Impacts and Implications: A lack of supervision and communication can result in accidents, injuries, and increased costs due to lost productivity and legal expenses.
Fatal Industrial Accidents: Prevention Strategies
Prevention is paramount in mitigating the risk of crushing accidents. By adopting a proactive approach to safety, employers can significantly reduce the potential for these tragic incidents.
1. Implement Comprehensive Safety Programs:
- Context: Establishing robust safety programs that address potential crushing hazards is crucial.
- Further Analysis: These programs should include regular hazard assessments, development and implementation of safety protocols, and comprehensive worker training on safety procedures, equipment use, and potential hazards.
2. Conduct Regular Equipment Maintenance and Inspections:
- Context: Regular inspections and maintenance of equipment are vital in identifying and addressing potential issues before they lead to accidents.
- Further Analysis: This includes checking for wear and tear, testing hydraulic systems, and ensuring safety guards are in place and functioning correctly.
3. Provide Appropriate Worker Training and Certification:
- Context: Adequately trained workers are better equipped to identify and mitigate potential hazards.
- Further Analysis: Training should cover safe work practices, equipment operation, emergency procedures, and specific safety protocols relevant to their roles.
4. Enforce Strict Safety Protocols and Procedures:
- Context: Implementing and strictly enforcing safety protocols are critical to ensuring compliance and preventing accidents.
- Further Analysis: This includes clear guidelines on equipment use, work zone procedures, emergency response, and reporting of unsafe conditions.
5. Promote a Culture of Safety and Awareness:
- Context: A culture of safety is essential, encouraging workers to prioritize safety, report concerns, and participate in safety initiatives.
- Further Analysis: This can be fostered through regular safety meetings, open communication, recognition programs for safe practices, and continuous safety improvement efforts.
Key Insights
- Fatal industrial accidents caused by crushing are a serious threat in many workplaces.
- Prevention is paramount and can be achieved through a multifaceted approach.
- A culture of safety and continuous improvement are essential for creating a safe working environment.
- Employers, workers, and safety professionals all have a responsibility to ensure worker safety.
FAQs About Fatal Industrial Accidents:
1. What are the most common types of industrial accidents involving crushing?
- Crushing accidents can occur in a wide range of industrial settings, including construction, manufacturing, mining, and transportation. Common scenarios include being trapped between machinery, struck by falling objects, or crushed by heavy equipment.
2. What are the long-term consequences of a crushing injury?
- Crushing injuries can have devastating long-term consequences, including permanent disabilities, chronic pain, and psychological trauma.
3. How can I report an unsafe work environment or potential hazard?
- Always report any unsafe conditions or potential hazards to your supervisor or safety manager immediately. Many companies have established reporting systems that allow workers to anonymously report concerns.
4. What are the legal implications of an industrial accident?
- Industrial accidents can have significant legal implications. Employers may be held liable for workplace safety violations, and victims or their families may be eligible for compensation.
5. What are the best resources for learning about workplace safety?
- Numerous organizations offer resources and training on workplace safety. OSHA (Occupational Safety and Health Administration) is a valuable resource providing guidelines, training materials, and information on workplace safety regulations.
6. How can I ensure my own safety in the workplace?
- Always follow safety protocols, use personal protective equipment, be aware of potential hazards, report unsafe conditions, and participate in safety training.
Tips for Preventing Crushing Accidents:
1. Follow safety procedures meticulously. Never take shortcuts or deviate from established safety protocols. 2. Use personal protective equipment (PPE) appropriately. Always wear the correct PPE for the task at hand, including safety glasses, hard hats, gloves, and footwear. 3. Be aware of your surroundings. Always be alert and aware of potential hazards, including machinery, moving objects, and work zones. 4. Report unsafe conditions immediately. Don't hesitate to report any potential hazard to your supervisor or safety manager. 5. Participate in safety training. Stay up-to-date on safety procedures and best practices by attending regular safety training sessions. 6. Communicate effectively. Always communicate clearly with co-workers about potential hazards and safety concerns. 7. Stay vigilant. Maintain a proactive approach to safety and never become complacent.
Summary of the Dangers of Crushing Accidents
Industrial accidents involving crushing are a stark reminder of the importance of workplace safety. These tragic events highlight the need for robust safety protocols, comprehensive training, and a culture of safety awareness. By implementing preventive measures and fostering a collaborative approach to safety, workplaces can significantly reduce the risk of crushing incidents.
Closing Message:
The loss of life due to crushing accidents is a devastating consequence of neglect and complacency. Let this tragic reality serve as a powerful reminder to prioritize safety and implement effective prevention strategies, safeguarding lives and ensuring a safer work environment for all.
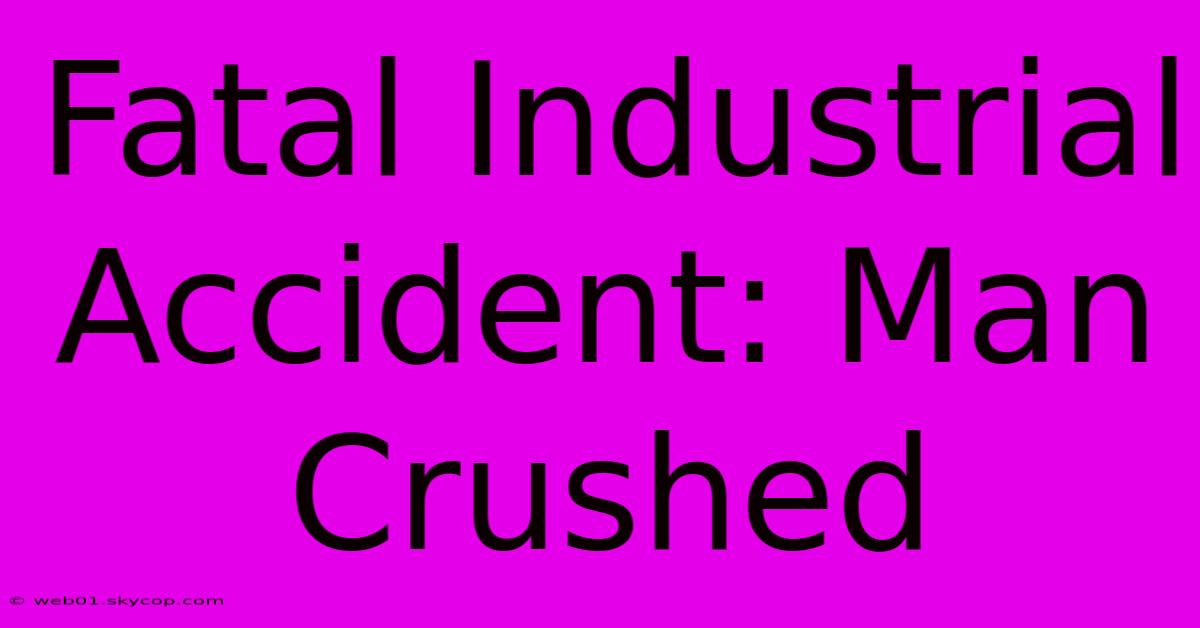
Thank you for visiting our website wich cover about Fatal Industrial Accident: Man Crushed. We hope the information provided has been useful to you. Feel free to contact us if you have any questions or need further assistance. See you next time and dont miss to bookmark.
Featured Posts
-
Hrm Remembrance Day Events Move Indoors
Nov 11, 2024
-
Olivia Rodrigo Op Affiche Rock Werchter
Nov 11, 2024
-
Ajax En Twente Delen Punten Wat Viel Op
Nov 11, 2024
-
Canada Post Honors Ontario Farmerettes
Nov 11, 2024
-
Bowl Projections Alabamas Destination
Nov 11, 2024